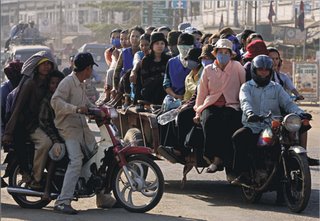
At a Cambodian factory that supplies some of the biggest names in British retailing, Nick Mathiason and John Aglionby hear pleas for a fairer deal for hard-pressed workers
Sunday April 23, 2006
The Observer (UK)
We do the same work as they do in other factories. They just pay us less,' said Nut Chenda. A complaint familiar to workers around the world, perhaps.
But Chenda may have a point. The Cambodian woman works as a machinist for the Fortune Garment and Woollen Knitting Factory, about 20 miles from the Cambodian capital, Phnom Penh. The Taiwanese-owned business sells garments to some of Britain's biggest retailers - among them, household names such as Next, Debenhams and BHS, headed by Philip Green.
Nut Chenda and all the workers The Observer spoke to last week outside the Fortune factory gates earn between $50 and $60 a month. Even in Cambodia - one of the world's poorest countries - that is low, especially as neighbouring factories, it is said, pay $90 to $100. Though Fortune maintains it pays a 'fair wage above the legal requirement'.
That may be true but it is only part of what appears to be a story of harsh conditions and aggressive responses to union activity. Almost all the 30 workers interviewed said conditions in the factory were poor. Most people work in rooms of 600 people, they maintained. 'There are not enough fans and only two doors, which are kept closed,' said Chenda.
'In the washing room there are lots of chemicals and the ceiling is not high, so it gets very hot and stuffy,' said another woman, who asked not to be named. 'We are given masks but they are not good enough, and we often suffer the effects of chemical inhalation.'
Yim Sarun works in the washing room. 'When the buyers come to inspect the factory the managers bring out the best equipment, like good gloves. They also open the doors and increase the ventilation. But no one is allowed to talk to visitors and after the buyers leave they close the doors and take away the [new] safety equipment.' Though workers admitted old and dangerous washing machines, which frequently caused accidents, were replaced last year.
Since 2004, union leaders say, 200 people out of a workforce of 2,500 have been dismissed for union activity. Next month the workers plan to strike, seeking reinstatement for a colleague dis-missed recently, allegedly for union activity, and demanding better pay.
'Over the past few years we have recognised unions and work with them,' said Fortune. 'There are three unions recognised in the factory. We have only sacked workers with the local courts' authorisation, and we follow local law.'
But the International Labour Organisation, a UN body aimed at improving working conditions, particularly in developing countries, has inspected it three times. In 2002, the ILO say, more violations were detected at Fortune than at almost any other Cambodian company it reviewed. In 2004 it had one of the worst records for implementing ILO recommendations, and received the greatest number of new recommendations.
Ros Harvey, the ILO's chief technical adviser in Cambodia, said: 'If they have not implemented our recommendations, they've got a problem; if they have only partly implemented them, they have still got a problem.' In the latest ILO report, published last August, Fortune had 39 outstanding issues to resolve, including sick pay, noise, ventilation, safety equipment, union activity and allegedly making employees injured at work pay for medicine. The ILO did point out that Fortune made progress on pay transparency and forced overtime, and an audit two weeks ago by consultancy Bureau Veritas has given the factory a clean bill of health.
But the general secretary of the International Textile, Garment and Leather Workers' Federation, Neil Kearney, last year wrote to Cambodian prime minister Hun Sen about labour issues which he said were 'threatening to undermine your country's pioneering efforts to put respect for core labour standards at the heart of your country's development strategy'. Kearney reaffirmed the position this weekend.
Though Fortune is just one case, the issue goes to the heart of contemporary retail, with pressure on suppliers from retailers wanting to offer low prices while increasing their own margins.
As prices in first world shops falls, consumer concern about how this is possible has risen. Dan Rees is director of the Ethical Trading Initiative, an industry-wide body of retailers and unions that promotes best practice throughout the supply chain. He said there had been progress among some retailers over health and safety issues and hours of work, but only up to a point. 'The best companies swim against the tide of globalisation,' Rees said. 'The biggest challenge is integrating ethical decisions in an environment of falling prices.'
It is a challenge perhaps too rarely met. But in recent years, media coverage of sweatshops in faraway places that produce footballs for Nike or T-shirts for Gap has forced giant retailers in particular to come clean and publish transparent auditing mechanisms as well as join industry-wide bodies to promote best practice. Numerous examples of company profits being dented by consumer boycotts on environmental or ethical issues explain why a new breed of 'reputation managers' has evolved over the past decade. The negative stories have also spawned audit firms that assess factories on behalf of retailers.
Maybe there is only so much retailers can do. And is it their responsibility to ensure that a factory they don't even own treats its workers fairly if no national laws are explicitly being broken? In the Fortune case, two of the companies involved - Debenhams and Next - are members of the Ethical Trading Initiative. They have received praise from that body for taking the issue seriously. Nevertheless, problems at the factory persist. The workers at Fortune struggling in a hot and noisy factory on low pay at the bottom of the supply chain need more than just a talking shop.
Philip Green's response: 'No cause for concern'
I was aware of the correspondence from 'Labour Behind the Label', which was passed to the relevant people at the time it was received. I have received extensive paperwork from my supplier and other parties, which I have studied to discover if there are any issues of substance and, if there are reasons why BHS and Arcadia should not do business with Fortune. I must tell you that I have found no issues which give me cause for concern. In coming to that view I have carefully taken into account all the points The Observer makes.
I have read the report of an audit conducted at the factory. Only trivial and irrelevant points, such as the absence of some smoking signs, are identified. I am confident that the points raised will be dealt with but I suspect this has been done. This audit was carried out by a company of international standing. On a previous occasion the head of the Ethical Trading Initiative was offered the opportunity to visit this factory. This was never taken. The ETI's failure to attend the premises may be explicable but it hardly fills me with confidence. I want to make it clear that the importance of manufacturer and supplier conduct is well understood by the boards of BHS and Arcadia. We are vigilant to ensure all our suppliers adhere to our codes of conduct.
But Chenda may have a point. The Cambodian woman works as a machinist for the Fortune Garment and Woollen Knitting Factory, about 20 miles from the Cambodian capital, Phnom Penh. The Taiwanese-owned business sells garments to some of Britain's biggest retailers - among them, household names such as Next, Debenhams and BHS, headed by Philip Green.
Nut Chenda and all the workers The Observer spoke to last week outside the Fortune factory gates earn between $50 and $60 a month. Even in Cambodia - one of the world's poorest countries - that is low, especially as neighbouring factories, it is said, pay $90 to $100. Though Fortune maintains it pays a 'fair wage above the legal requirement'.
That may be true but it is only part of what appears to be a story of harsh conditions and aggressive responses to union activity. Almost all the 30 workers interviewed said conditions in the factory were poor. Most people work in rooms of 600 people, they maintained. 'There are not enough fans and only two doors, which are kept closed,' said Chenda.
'In the washing room there are lots of chemicals and the ceiling is not high, so it gets very hot and stuffy,' said another woman, who asked not to be named. 'We are given masks but they are not good enough, and we often suffer the effects of chemical inhalation.'
Yim Sarun works in the washing room. 'When the buyers come to inspect the factory the managers bring out the best equipment, like good gloves. They also open the doors and increase the ventilation. But no one is allowed to talk to visitors and after the buyers leave they close the doors and take away the [new] safety equipment.' Though workers admitted old and dangerous washing machines, which frequently caused accidents, were replaced last year.
Since 2004, union leaders say, 200 people out of a workforce of 2,500 have been dismissed for union activity. Next month the workers plan to strike, seeking reinstatement for a colleague dis-missed recently, allegedly for union activity, and demanding better pay.
'Over the past few years we have recognised unions and work with them,' said Fortune. 'There are three unions recognised in the factory. We have only sacked workers with the local courts' authorisation, and we follow local law.'
But the International Labour Organisation, a UN body aimed at improving working conditions, particularly in developing countries, has inspected it three times. In 2002, the ILO say, more violations were detected at Fortune than at almost any other Cambodian company it reviewed. In 2004 it had one of the worst records for implementing ILO recommendations, and received the greatest number of new recommendations.
Ros Harvey, the ILO's chief technical adviser in Cambodia, said: 'If they have not implemented our recommendations, they've got a problem; if they have only partly implemented them, they have still got a problem.' In the latest ILO report, published last August, Fortune had 39 outstanding issues to resolve, including sick pay, noise, ventilation, safety equipment, union activity and allegedly making employees injured at work pay for medicine. The ILO did point out that Fortune made progress on pay transparency and forced overtime, and an audit two weeks ago by consultancy Bureau Veritas has given the factory a clean bill of health.
But the general secretary of the International Textile, Garment and Leather Workers' Federation, Neil Kearney, last year wrote to Cambodian prime minister Hun Sen about labour issues which he said were 'threatening to undermine your country's pioneering efforts to put respect for core labour standards at the heart of your country's development strategy'. Kearney reaffirmed the position this weekend.
Though Fortune is just one case, the issue goes to the heart of contemporary retail, with pressure on suppliers from retailers wanting to offer low prices while increasing their own margins.
As prices in first world shops falls, consumer concern about how this is possible has risen. Dan Rees is director of the Ethical Trading Initiative, an industry-wide body of retailers and unions that promotes best practice throughout the supply chain. He said there had been progress among some retailers over health and safety issues and hours of work, but only up to a point. 'The best companies swim against the tide of globalisation,' Rees said. 'The biggest challenge is integrating ethical decisions in an environment of falling prices.'
It is a challenge perhaps too rarely met. But in recent years, media coverage of sweatshops in faraway places that produce footballs for Nike or T-shirts for Gap has forced giant retailers in particular to come clean and publish transparent auditing mechanisms as well as join industry-wide bodies to promote best practice. Numerous examples of company profits being dented by consumer boycotts on environmental or ethical issues explain why a new breed of 'reputation managers' has evolved over the past decade. The negative stories have also spawned audit firms that assess factories on behalf of retailers.
Maybe there is only so much retailers can do. And is it their responsibility to ensure that a factory they don't even own treats its workers fairly if no national laws are explicitly being broken? In the Fortune case, two of the companies involved - Debenhams and Next - are members of the Ethical Trading Initiative. They have received praise from that body for taking the issue seriously. Nevertheless, problems at the factory persist. The workers at Fortune struggling in a hot and noisy factory on low pay at the bottom of the supply chain need more than just a talking shop.
Philip Green's response: 'No cause for concern'
I was aware of the correspondence from 'Labour Behind the Label', which was passed to the relevant people at the time it was received. I have received extensive paperwork from my supplier and other parties, which I have studied to discover if there are any issues of substance and, if there are reasons why BHS and Arcadia should not do business with Fortune. I must tell you that I have found no issues which give me cause for concern. In coming to that view I have carefully taken into account all the points The Observer makes.
I have read the report of an audit conducted at the factory. Only trivial and irrelevant points, such as the absence of some smoking signs, are identified. I am confident that the points raised will be dealt with but I suspect this has been done. This audit was carried out by a company of international standing. On a previous occasion the head of the Ethical Trading Initiative was offered the opportunity to visit this factory. This was never taken. The ETI's failure to attend the premises may be explicable but it hardly fills me with confidence. I want to make it clear that the importance of manufacturer and supplier conduct is well understood by the boards of BHS and Arcadia. We are vigilant to ensure all our suppliers adhere to our codes of conduct.
No comments:
Post a Comment